GESTIONE INVECCHIAMENTO E INTEGRITÀ DI IMPIANTI INDUSTRIALI
ENCOTES INGEGNERIA ha sviluppato un’approccio sistematico “Inspection Plan Management” per la gestione delle condizioni di invecchiamento e integrità degli impianti industriali mediante servizi di Risk Based Inspection (RBI), Planning and Management per le tubazioni, i serbatoi e i recipienti a pressione.
L’obiettivo del servizio è quello di fornire alle aziende uno strumento operativo al fine di gestire in modo sicuro il processo
di invecchiamento e degrado di attrezzature e impianti critici. Il problema diventa particolarmente importante per gli impianti a rischio di incidente rilevante (impianti “Seveso”), nei quali l’invecchiamento può diventare una possibile causa iniziatrice di meccanismi di degrado e di rilasci di sostanze pericolose dove ogni fattore che lo determina
può essere definito come un “fattore di rischio”. In Italia, il D.Lgs. 105/2015, che recepisce la Direttiva 2012/18/EU (Seveso III), introduce l’obbligo di adottare piani di
monitoraggio e controllo dei rischi legati all’invecchiamento di attrezzature e impianti, che tenga conto dei meccanismi di deterioramento presenti, inclusi corrosione interna ed esterna, erosione, fatica termica e meccanica.
L’approccio utilizzato è in accordo a standard riconosciuti quali API 580, 581 e la norma UNI EN 16991 Risk Based Inspection.
“INSPECTION PLAN MANAGEMENT” è la strategia d ENCOTES INGEGNERIA per lo sviluppo di programmi di ispezione e manutenzione ottimizzati e convenienti in un contesto di invecchiamento di un impianto industriale o di una attrezzatura.
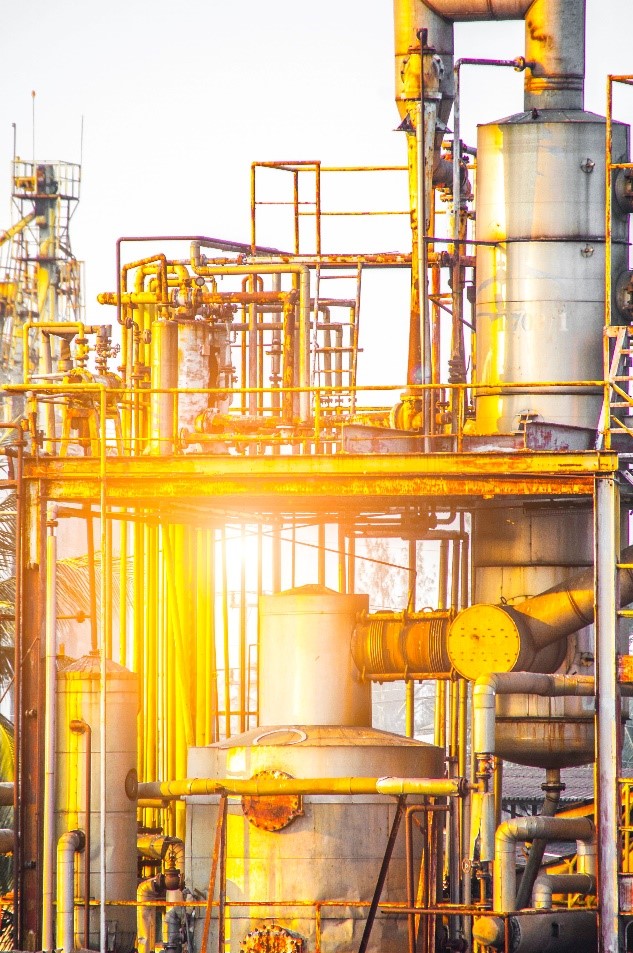
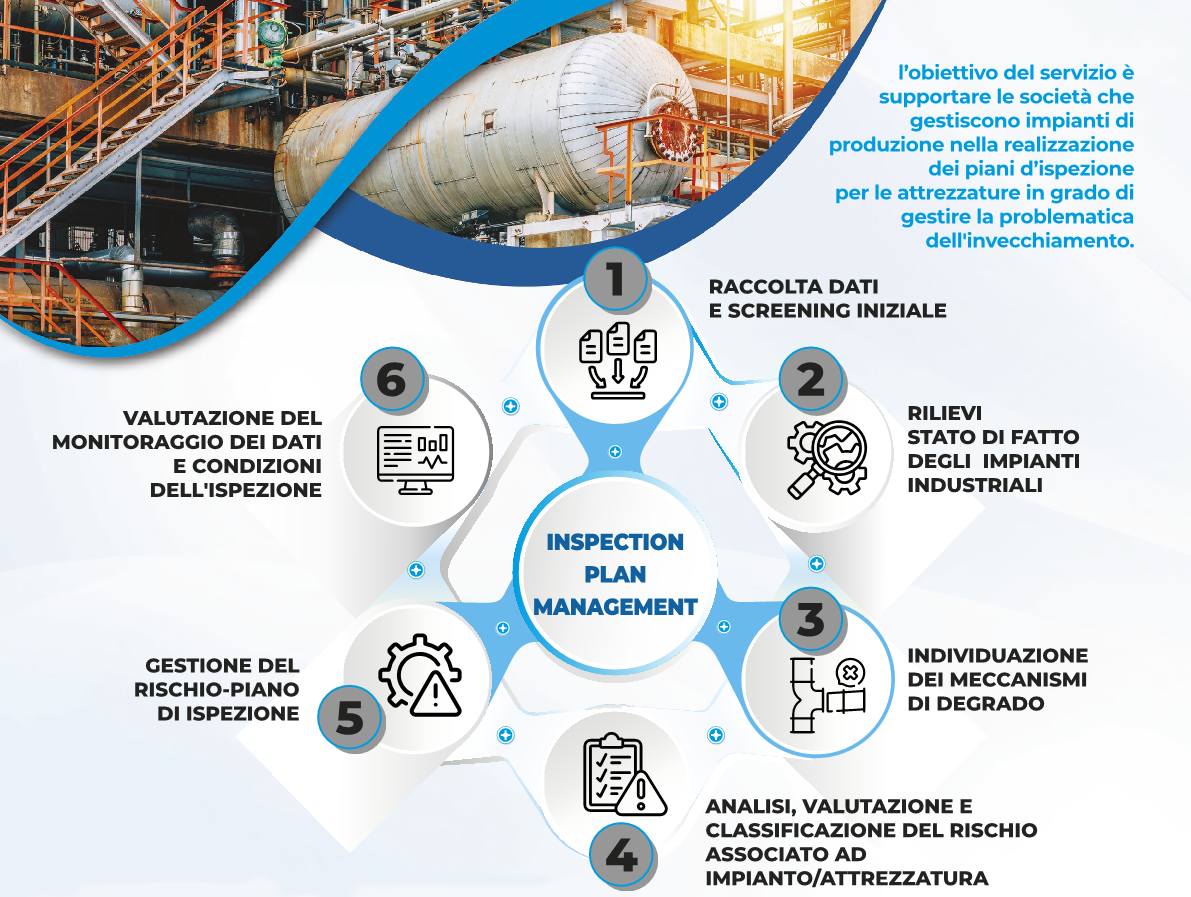
1 RACCOLTA DATI E SCREENING INIZIALE
Questa fase consiste nella creazione di un data-base contenente informazioni necessarie per lo studio, come materiale delle apparecchiature, sovraspessore di corrosione, coibentazione, dati di progetto, storico ispettivo, ecc.
2 RILIEVI STATO DI FATTO DEGLI IMPIANTI INDUSTRIALI
Rilievi in campo con metodologia LASER SCANNER 3D fondamentale al supporto delle attività di monitoraggio e manutenzione degli impianti industriali. L’attività può essere svolta quando la documentazione tecnica disponibile risulta incompleta e inattendibile a causa delle modifiche apportate nel corso degli anni e mai registrate sui documenti originali. Il rilievo con laser scanner riscontra lo stato di fatto dell’impianto completo di tutte le strutture, recipienti, tubazioni e tutte le dotazioni collegate (pompe, motori, valvole, strumenti, quadri elettrici, connessioni elettro-strumentali, ecc.) con conseguente elaborazione in 2D e 3D della documentazione tecnica.
3 INDIVIDUAZIONE DEI MECCANISMI DI DEGRADO
Individuazione ed analisi dei meccanismi di degrado specifici agenti sull’attrezzatura (basandosi sulle sostanze, sulle loro condizioni e sullo stato dei materiali). Analisi dei meccanismi di degrado esistenti o che potrebbero generarsi nel tempo.
4 ANALISI, VALUTAZIONE E CLASSIFICAZIONE DEL RISCHIO ASSOCIATO AD IMPIANTO/ATTREZZATURA
Utilizzo di metodi basati su procedure specifiche per la programmazione delle ispezioni, quali ad esempio API RP 581, oppure metodi di analisi del rischio, quali Fault Tree Analisys (FTA), Event Tree Analysis (ETA), Failure Mode and Effect Analisys (FMEA), Failure Mode, Effect and Criticality Analisys (FMECA), ecc.
Elaborazione di report di valutazione rischi con calcolo di vita consumata per effetto del meccanismo di danno individuato ( es. fatica, corrosione, ecc.). Elaborazione di relazione di calcolo dello spessore minimo (in mancanza degli spessori minimi di progetto) dell’attrezzatura in valutazione secondo specifici codici di calcolo.
5 GESTIONE DEL RISCHIO-PIANO DI ISPEZIONE
Il rischio relativo all’attrezzatura viene gestito attraverso l’implementazione del piano di ispezione, avente la finalità di gestire il rischio portandolo e mantenendolo ad un livello accettabile.
La strategia ispettiva delle attrezzature si basa su una serie di attività tese a mettere in atto un piano articolato di controlli che consenta di verificarne l’integrità strutturale e di controllare lo stato di avanzamento del degrado dei loro principali componenti in modo da rendere minimo il rischio di fuoriuscite del prodotto contenuto che potrebbero provocare danni all’uomo, all’ambiente e alle cose.
Definizione dei controlli non distruttivi (CND) in funzione dell’invecchiamento dell’attrezzatura.
Personalizzazione delle tecnologia ispettive, oltre all’ispezione visiva, interna o esterna, i meccanismi di degrado possono essere identificati tramite le tecniche di CND, come ad esempio: Ispezione visiva (VT) Liquidi penetranti (PT) Magnetoscopia (MT) Ultrasuoni (UT), analisi metallografiche microstrutturali, ecc. Identificazione dei punti di rilievo ed eventuale etichettatura su ogni attrezzatura da riportare su elaborati grafici al fine di ottenere uno storico ispettivo degli impianti.
Elaborazione dei report dei controlli non distruttivi (CND).
6 VALUTAZIONE DEL MONITORAGGIO DEI DATI E CONDIZIONI DELL’ISPEZIONE
Analisi dei risultati.
Valutazione dei dati.
Supporto e consulenza per il funzionamento ed eventuali azioni correttive.
Aggiornamento e conservazione dei dati (ore di funzionamento, cicli di lavoro, variazioni operative, ecc.).
Programmazione delle attività future attraverso l’implementazione di specifici piani ispettivi.
SCARICA LA SCHEDA DEL SERVIZIO